





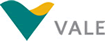

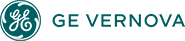









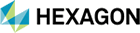


During the recent ARC Industry Forum, L&T Technology Services (LTTS) provided a workshop on the digital enterprise. The introduction of Industry 4.0 initiated the rise of smart enterprise providing a competitive edge to those who embrace it. But many companies have struggled with its digital transformation being limited to a few use cases and have been unable to scale effectively. The workshop helped demystify the Industry 4.0 challenge and provided an evaluation opportunity for the workshop attendees to assess their Industry 4.0 readiness against the industry benchmarks. Their evaluations were compared with LTTS’ maturity index which is created based on data collected from an Industry 4.0 survey that covered more than 100 global conglomerates.
The workshop started with a survey among the attendees for gathering their benchmark data and was followed later with an extensive Q&A panel discussion.
Prior to the workshop, LTTS surveyed manufacturing executives regarding their progress with Industry 4.0. We were able to compare those who answered the survey with those attending the Forum workshop. The table provides few questions and the responses that caught ARC’s attention.
Interesting contrast in the answers to this question. Those answering the general survey need help scaling the digital at an enterprise level whereas the ARC Forum attendees have moved passed this issue and are more focused on extending best practices across their business. However, delivering ROI and addressing gaps between IT and Engineering for running PLM systems remain common challenges across both the groups.
After identifying a use case, the next hurdle becomes determining the ROI. Again, the ARC Forum attendees are ahead of the general industry participants. ARC has observed the tendency for executives to focus on internal costs as the basis for return on investment. Unfortunately, this approach is typically weak. The lack of follow-through to cut headcount (people given other assignments) creates the senior executive viewpoint that the project failed (no ROI) and a skepticism for other Industry 4.0 projects.
A better source of ROI is the effect on revenue and inventory. For example, unplanned downtime interrupts production causing lost revenues. Preventing these lost revenues nearly always easily justifies an investment in predictive maintenance and the associated Industry 4.0 business processes to fix the issue prior to equipment failure. The increase in revenues gets executive support and interest in other Industry 4.0 projects.
Both the general industry and forum attendees have an issue with the gap between IT and engineering. Unfortunately, a major gap exists in the measurements and KPIs. For the business systems like ERP, IT tends to focus on the financial reporting. If that is broken, the executives that sign the annual report can be sent to jail. For other systems, the focus tends to become reduced operating and support costs – which includes the critical desktop systems used by engineering. Issues with these engineering technology (ET) systems have less of an effect on the measurements for IT compared with cost control. More mature organizations integrate IT, ET and operating technology (OT) – which is a theme in recent ARC Forums.
The panel was moderated by Neelakandan Sharma, AVP Digital Advisory Services, LTTS, and the workshop panel members included:
Neelakandan continued with the issue of identifying ROI among the panel members. He asked, “How do you build an ROI and pragmatic applications? What are the common priorities for customers in the digital manufacturing journey?”
Ralph replied that there is a tendency to focus on the IoT technology rather than finding practical applications. A much higher success rate occurs when focused on a recognized problem and an associated solution. Initially, success was found with applications for predictive maintenance using small data from a particular piece of equipment to monitor the health of that equipment and take corrective action when detecting deterioration. Small data is much easier to manage than big data.
Representative from the air conditioning systems manufacturing company added that people can be caught up in technology for the sake of technology and look for a place to apply it. Instead, his company’s approach is to identify a problem and its solution. Then, sell executive management on the value of that solution. The reason why many are not scaling as quickly with technology is because some plants are still at Industry 3.0. There, his company gets back to the basics of lean manufacturing one-on-one. Do we have a value stream map? Do we have standard work? How do we attain our schedule? Are you running efficiently? Technology is typically applied after the system is lean and optimized. A value stream map can be used to identify where technology can be applied to improve the overall process performance.
Prabhakar agreed to this point and mentioned that technology may not be needed for process optimization. Start with understanding the plant's pain points and sources of waste before applying software or other technology. Often, there are incremental solutions that do not cost much. From a lean standpoint, understand how things flow, and listen to the “voice of the process.” When you hear the process, you understand the pain points. When you understand the pain points of the plant, you gain an understanding of the fundamental needs of the plant and this is an essential quality for leaders in plant operations. The business wants efficiency, productivity, and attainment of a schedule.
L&T Technology Services Limited is focused on Engineering and R&D services and a listed subsidiary of Larsen & Toubro Limited. LTTS offers consultancy, design, development, and testing services across the product and process development life cycle for transportation, industrial products, plant engineering, semiconductors, consumer electronics, medical devices, telecommunications, and oil & gas.